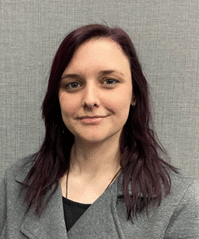
“The Impact of Data Analytics on Decision-Making in Operations Management” an opinion piece by Dr Amy Long, Chief Operating Officer
In today’s fast-paced and competitive business environment, operations managers are under constant pressure to make decisions that improve efficiency, reduce costs, and enhance customer satisfaction. Organisations cannot simply do better than before; they must seek innovative solutions to drive customer satisfaction and profit margins. Enter data analytics—a powerful tool that is transforming operations management by enabling data-driven, informed decision-making.
This blog explores how data analytics can empower operations managers to optimise processes, predict future trends, and deliver exceptional customer experiences and service. We’ll dive into key areas such as predictive analytics, real-time monitoring, and the role of big data in revolutionising operations management.
The Rise of Data-Driven Decision-Making in Operations Management
The Rise of Data-Driven Decision-Making in Operations Management
Data analytics has become a cornerstone of modern operations management. By collecting, analysing, and interpreting data from various sources, organisations can uncover actionable insights that were previously hidden. Think of your organisations Net Promoter Score as one source of data which can provide key insights into your customer experience and where your operational issues lie. Data-driven decision-making allows operations managers to:
- Identify inefficiencies and bottlenecks in processes.
- Forecast demand and allocate resources more effectively.
- Respond to customer needs in real-time.
- Reduce risks and improve overall operational performance.
The power of data analytics lies in its ability to provide objective, evidence-based insights, replacing guesswork with precision. Consider seasonal periods in the retail industry which can cause bottlenecks, pressures and customer unhappiness. Through the use of data analytics, process improvements can easily be identified and actioned timeously to ensure uninterrupted service delivery.
Predictive Analytics: Anticipating the Future
Predictive Analytics: Anticipating the Future
One of the most exciting applications of data analytics in operations management is predictive analytics. Using historical data, statistical algorithms, and machine learning techniques, predictive analytics helps managers forecast future trends and make proactive decisions.
Key Benefits of Predictive Analytics:
Key Benefits of Predictive Analytics:
1. Demand Forecasting:
By analysing past sales data, seasonal trends, and external factors (like market conditions or weather), predictive analytics enables managers to anticipate demand fluctuations. This ensures optimal inventory levels, reducing the risk of stockouts or overstocking. Think of Summer and Winter in South Africa, and the seasonality of goods and services that come with these periods in the year.
2. Maintenance Planning:
Predictive analytics can identify patterns in equipment performance, allowing managers to schedule maintenance before machinery fails. This minimises downtime and extends the lifespan of critical assets.
3. Risk Mitigation:
Predictive models can assess potential risks in supply chains, such as delays or disruptions, and suggest alternative strategies to avoid costly setbacks. For example, companies like Amazon use predictive analytics to manage inventory across their vast supply chain, ensuring that products are always available when and where customers need them.
Real-Time Monitoring: Staying Ahead of the Curve
Real-Time Monitoring: Staying Ahead of the Curve
In addition to predicting future events, data analytics enables real-time monitoring of operations. With the help of IoT (Internet of Things) devices, sensors, and advanced analytics platforms, businesses can track key performance metrics and respond to issues as they arise.
Applications of Real-Time Monitoring:
- Supply Chain Visibility:
Real-time data on shipments, inventory levels, and supplier performance allows managers to identify and resolve issues instantly, ensuring seamless operations. - Production Line Optimisation:
Sensors on factory floors can monitor equipment performance, energy usage, and production output in real-time, helping managers address inefficiencies and maintain quality standards. - Customer Experience:
Real-time analytics of customer interactions—such as website activity or call centre performance—enables businesses to provide immediate support and improve satisfaction.
For instance, logistics companies like Takelot and Courier Guy use real-time tracking to monitor package deliveries, ensuring on-time performance and providing customers with live updates.
Big Data Unlocking New Opportunities
The explosion of data generated by businesses today—often referred to as big data—has created unprecedented opportunities for operations management. Big data encompasses vast volumes of structured and unstructured information, from transactional records to social media posts and IoT sensor readings.
How Big Data Optimises Operations:
How Big Data Optimises Operations:
1. Process Optimisation:
By analysing massive datasets, businesses can identify inefficiencies and implement improvements across their operations. For example, big data can reveal patterns in production delays or employee productivity, leading to targeted interventions.
2. Personalised Customer Experiences:
Big data analytics enables businesses to understand customer preferences and behaviours on a granular level. This allows for personalised marketing, tailored product recommendations, and improved service delivery.
3. Enhanced Decision-Making:
Big data provides a holistic view of operations, combining insights from multiple sources (e.g., supply chain, sales, and customer feedback). This comprehensive perspective helps managers make well-rounded decisions that align with organisational goals.
Companies like Netflix and Youtube leverage big data to optimise their content delivery and recommend shows/videos based on user preferences, improving customer satisfaction and retention.
iQ Academy: Operations Management Short Course
iQ Academy: Operations Management Short Course
Grasping data analytic processes and interpretations can take time and practice. Studying a course which equips you with these skills, bridges the gap between formal and existing knowledge. This course enhances skills related to data-driven decision-making by equipping learners with tools and methodologies to assess process efficiency, identify bottlenecks, and apply forecasting methods. Through units like “Forecasting and Scheduling” and “Monitoring and Evaluation of Operations,” students learn to collect, analyse, and interpret data to optimise resource allocation, improve operational efficiency, and align strategies with measurable business objectives.
Additionally, the application of Total Quality Management (TQM) and Lean Management principles teaches learners to use data to identify areas for improvement, reduce waste, and enhance productivity, enabling informed and effective decision-making in operational contexts.
Conclusion
Conclusion
Data analytics is no longer a luxury—it’s a necessity for modern operations management. By harnessing the power of predictive analytics, real-time monitoring, and big data, operations managers can make smarter, faster, and more informed decisions. These tools not only optimise processes and reduce costs but also enhance customer satisfaction, giving businesses a competitive edge in an increasingly data-driven world.
As technology continues to evolve, the role of data analytics in operations management will only grow, offering new opportunities to innovate and excel. The question is no longer whether to embrace data analytics, but how quickly organisations can integrate it into their operations to stay ahead of the curve.